Our Products
Copper Base Alloy Foundry
Toyo Metallurgicals Ltd. is your trusted partner in the Copper Base Alloy Foundry industry. Since 1963, we have been dedicated to manufacturing exceptional metallurgical chemicals designed to meet the unique requirements of Copper Base Alloy Foundries such as high conductivity copper, aluminum bronze, leaded bronze, gunmetal, phosphorus, bronze, manganese bronze and brasses.
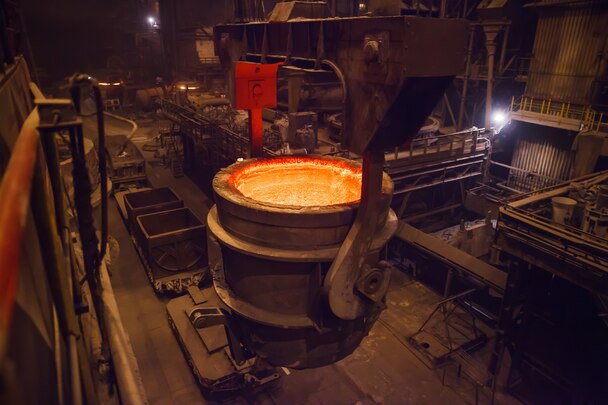
Fluxes for Copper & Nickel Alloys
|
||
---|---|---|
Product
|
Recommended For
|
Advantages
|
Coppercleaner standard powder or Cleanex Block B Briq Coppercleaner-20 powder, Coppercleaner-20 Briq (oxidizing fluxes for covering and cleaning (Copper and Nickel Alloys)).
|
Copper alloys containing Tin and Nickel will readily absorb hydrogen from combustion products, humid atmosphere and other source of moisture. When metal containing dissolved hydrogen the gas appears as voids or cavities in the casting. Oxidising coppercleaner fluxes prevent hydrogen pick-up, cleans metal and give pressure tight casting with improved mechanical properties.
|
1.Provides the two-fold action scavenging the metal and providing a protective cover.
2.Prevents hydrogen pick-up and cleans metal. 3.Improves physical properties of the metal and ensures sound and pressure tight castings. |
Metalcleaner 49 Metalcleaner 8 (Reducing fluxes for covering and protecting Copper and Copper Zinc alloys)
|
Melting copper-zinc alloys require non oxidizing conditions and also need additional precaution to prevent zinc fuming. Alloys poured Without covering fluxes show abnormally high metal content in the dross and often require the addition of alloying elements.
|
1.Prevents absorption of harmful gases.
2.Melting loss and Zinc fuming are significantly reduced. 3.Metal-free drosses are obtained 4.Slag build-up on crucibles and furnace linings is greatly reduced. |
Alberol\Alberol2 (Flux for covering and reducing oxide formation and inclusions in Aluminium, Manganese and Silicon Bronzos)
|
During melting, Copper base Alloys containing Aluminium, Mangananese and silicon have great affinity for oxygen which forms large amounts of oxides in the form of heavy dross. When the metal solidifies these insoluble oxides develop a fine film at the grain boundaries which impairs proper feeding of the casting and weakens the Alloy's structure. In subsequent fabrications these oxides are revealed as long films in extrusions and rolled sheet, shortening die life and resisting movement through the extrusion press, in forging the oxides induce cracking.
|
1.Effectively prevents formation of harmful oxides of Aluminium, Manganese or Silicon.
2.Forms a protective cover that minimises oxidation and Zinc fuming. 3.Increases fluidity and feeding properties. 4.Reduces dross formation and crucible build-up. 5.Avoid metal content skimmings. 6.Does not alter alloy compositions |
T-Logas (for easy and efficient removal of Hydrogen from all Copper base and Nickel base alloys).
|
In the production of pressure tight castings to with-stand high pressures, removal of all traces of gas is essential. Degassing treatment is mandatory. When the original charge material contains foreign matter or is having contaminated with grease and oil, Logas removes dissolved gases and suspended impurities in one operation.
|
1.Eliminates gas porosity and casting leakage under pressure.
2.Ensures homogenous alloy with improved mechanical properties 3.Promotes better feeding of castings |
De-oxidising Tubes (For controlled de-oxidation and increased fluidity of copper and nickel alloys)
|
Different alloys require different De-oxidiants. De-oxidising tubes are available in different grades containing the appropriate De-oxidents like Phosphor cooper, Calcium Boride, Bron Managanes and Magnesium in proper quantities. Ingredients are in fine granular form and most effective remover of oxygen and oxides
|
1.Provides accurate control of de-oxident.
2.Easy to use. 3.Prevents waste of expensive material. 4.Granular form provides fast and complete removal of oxides and excess oxygen. 5.Prevents porosity and increases fluidity of metal. 6.Sulphur embrittlement is prevented in Nickel Alloys. 7.Ensures production of sound pressure tight castings. |
Improval A.C./A.C.2 (For fast and efficient removal of Aluminium from Copper and Nickel Alloys)
|
Alloys where Aluminium is not an alloying element, Its presence even in traces substantially reduces mechanical properties and causes the castings to leak under pressure. This is because the Aluminium impurity oxidizes readily to form dross and inclusions which locate themselves at the grain boundaries, weakening the structure and causing porosity.
|
1.Removes Alumlnium and its oxide efficiently.
2.Does not introduce other impurities 3.Assures slag free melt. 4.Forms covering slag that reduces oxidisation losses and increases fluidity |
Metal Cleaner (Standard) or Cleanex Block A
|
Alloys poured without covering fluxes show abnormal high metal content in dross and often required the addition of alloying elements
|
1.Oxidation and fuming of Zinc restricted.
2.Prevent absorption of harmful gases. 3.Minimum melting loss and clean alloy with no slag inclusion. 4.Slag is free from trace of metal. |
Metal Cleaner Super Pink (Pink colour powder)
|
Scavenging Flux recommended for Brass and Gun Metal
|
Minimum melting loss reduce melting time & Maximum purification of metal
|
Coatings
|
||||
---|---|---|---|---|
COATING & DRESSING
|
Form Supplied
|
Refractory Material
|
Carrier
|
Method of Applying
|
MOULDCOTE 101
|
Powder paste / R.F.U.
|
Graphite
|
Alcohol
|
B.S.
|
MOULDCOTE 101 (Air Cure)
|
R.F.U.
|
Graphite
|
Solvent
|
D.B.S.
|
ZIRCON COTE 101
|
Powder paste/R.F.U.
|
Zircon
|
Alcohol
|
B.S.
|
ZIRCON COTE W/B
|
Powder paste/R.F.U.
|
Zircon
|
Water
|
B.S.
|
MOULDCOTE GZW
|
Paste
|
Graphite/Zircon
|
Water
|
B.S
|
MOULDCOTE 60
|
Powder
|
Graphite/Talc/Ollvine
|
Water
|
B.S.
|
MODULCOTE 14-W
|
Powder
|
Mica
|
Water
|
B.S.
|
MODUL PAINT 212
|
Paste
|
Graphite/Ceramic
|
Water
|
B.S.
|
Moldcote 510 (Diluter for alcohol base coating)
|
Liquid
|
|||
D- Dipping
B- Brushing S- Spraying R.F.U.-Ready for used |
Powder coatings must be made into a paste prior to application. After as 24hr. bulge they may be used in the necessary viscosity. Application of two thin layers instead of one thick layer is recommended. Alcohol based coatings should be used for mould & cores containing P.F. resin alkyd base and Co2 cured binder.
|
Feeding Aids
|
|
---|---|
Ladcov
|
For Ladle Insulation
Hot Topping Compounds for insulating the surface of melt. Exothermic antipiping compounds for increased feeding efficiency Expandable antipiping compound |
Ex feed NF
|
Highly Exothermic material producing molten metal for efficient feeding of Steel Castings
|
Exothermic/ Insulating sleeves:
|
Riser sleeves for exothermic & insulating action for efficient feeding & improvement in the yield.Toyoform Sleeves : Modified sleeves for tailormade applications.
|
Slag Coagulants
|
|
---|---|
Slax P Blue
|
Slag Coagulant
|
Core and Mould Compounds
|
|
---|---|
Core Oil RTS 50
|
Core oven baking type core oil
|
Core Oil A1 Sp
|
Linseed Base
|
Air Setting Core Oil
|
Air drying core oil. No need to bake
|
SS Liquid
|
Sodium Silicate
|
Satyosil
|
Sodium Silicate with breakdown agent
|
Monosil
|
Sodium Silicate with a superior breakdown agent
|
Breakdown Agent
|
In Powder form for CO2 Cores
|
Liquid Collapsible Agent
|
In Liquid form for CO2 Cores
|
DBA 55
|
Accelerator for Sodium Silicate process, a substitute for CO2 gas.
|
Sand Mix Super Pink
|
Green Sand Binder, giving excellent green as well as hot tear strength.
|
Anti Scabbing Agent
|
To prevent scabbing in moulds
|
YD Core Binder
|
Superior binder for dry strength.
|
Air Set NBS
|
Air setting binder
|
DBA 55
|
Accelerator for Sodium Silicate process, a substitute for CO2 gas.
|
Core Grip
|
Core Joining Agent
|
Core Grip Hot to Hot
|
Core Joining Agent for Hot Box Process
|
Core Fill Paste
|
For core repairs, patching, filler for parting lines.
|
Seprol GSM
|
Pattern release agent for green sand moulding
|
Seprol GS
|
Pattern release agent for green sand moulding
|
Seprol 96
|
Parting agent for cold box dies.
|
Seprol 98
|
Parting agent for cold box without oil residue
|
Seprol SM
|
Parting agent for hot box
|
Seprol 80 SM
|
Waterbase parting agent for hot box
|
Seprol CBX
|
Cleaning agent for coldbox and hot box process
|
Stripcote Silver
|
Release agent for any pattern for green sand, CO2 or any resin bonded sand
|